Projects
SELECT PROJECTS
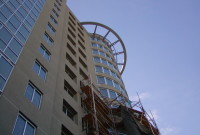
SOMA HIGH RISE – ASTM E1105 water testing without differential pressure and AAMA 501.2 nozzle tests were performed on the plaster wall system, windows and aluminum curtain wall system at these high-rise and low-rise residential structures in South of Market, San Francisco. Water infiltration was noted through the curtain wall system and adjacent to the windows within the cement plaster wall system. ACI facilitated the testing and evaluation of the source of the problems through isolation testing of the various exterior products. Eventual repairs consisted of the installation of an elastomeric coating system to minimize water entry at deficiencies between the cement plaster and windows. Additional repairs were also performed within the window wall systems.
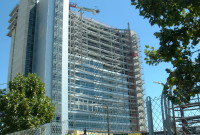
PENTHOUSE ROOF EVALUATION & REMEDIATION – Provided third party observations for installation of a hot rubber asphalt roof system being installed on the upper roof and mechanical penthouse of this high rise structure. Problems existed with the use of a non-vented steel deck with a lightweight insulating concrete fill. Installation of the hot rubber roof system was occurring during hot weather conditions in mid- summer. Moisture trapped within the concrete created blisters within the newly installed hot rubber roof system. Moisture vapor was trying to escape the concrete, as it could not escape through the un-vented deck. Repairs consisted of additional venting of roof system and special primers to inhibit moisture vapor drive into the newly installed membrane.

SAN JOSE AIRPORT TESTING – Coordinated the water penetration resistance testing of a 6,500 square-foot skylight system constructed of aluminum framing and glass panels. Designed and fabricated a rolling water-spray system to facilitate pressure differential and ambient pressure testing safely and efficiently.
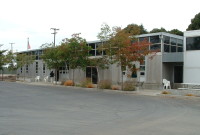
EAST BAY MUD FACILITY – Incremental water tests were performed on this commercial services building for an East Bay Municipal Utility district. Historic infiltration had been occurring on this structure following conversion from a utility building to offices. Various exterior wall components, consisting of metal panels, aluminum windows, roofing and doors, were water tested independently of each other to track the sources of water infiltration. Once the testing was completed, the various building components were disassembled to determine the as-built construction and the methodology for repairs. Detailed drawings and repair specifications were produced along with bid documents to provide the building owners with materials to solicit competitive bidding.
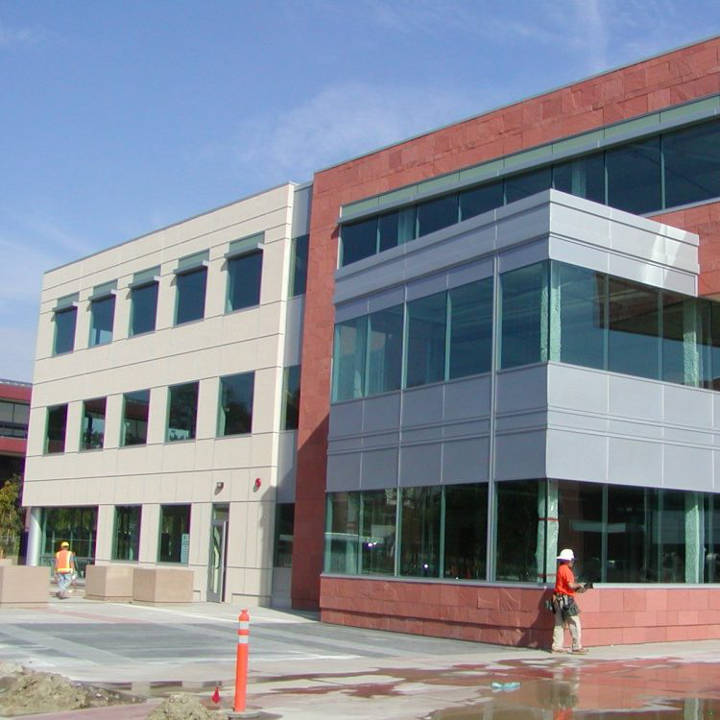
SOLANO BEACH OFFICE PARK – Provided assistance to plastering contractor regarding water infiltration problems in a newly constructed office park in Solano Beach, California. Exterior building components consisted of cement plaster (stucco), masonry cladding, aluminum panel cladding, storefront window systems, and various aluminum cladding components. Water infiltration was noted through the masonry wall and plaster wall systems, which incorporate a cavity drainage system as opposed to the aluminum panels, which created a barrier system. The heavy reliance on aluminum reveals within the cement plaster allowed excess water into cavity drainage system.
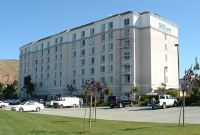
MID-RISE HOTEL – Performed ASTM E1105 differential performance water tests on a mid-rise hotel located in South San Francisco. The purpose of the performance water tests were to assist in evaluation of historic water infiltration problems around the window systems at guest rooms, primarily on the south and west elevations of the structure. Initial tests were performed to establish the failure mechanisms, and then compliance tests were performed following mock-up repairs. Test reports were provided following completion of testing.
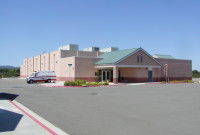
SANTA ROSA POLICE TRAINING FACILITY – Provide evaluation support for project design architectural firm for recently completed police training facility at Santa Rosa Junior College. Initial evaluation processes consisted of water testing at the roof system and vertical walls of this concrete tilt-up building structure. Water entry noted through the tilt-up concrete column caps and through concrete cracks in the tilt-up panels, even though the panels had previously been coated with an elastomeric coating system. Determinations were made that the column caps were not adequately caulked with sealant at the interface with the tilt-up panels. Some wall cracks were noted telegraphing through the elastomeric coating system. Recommendations were made to install sealants at the column cap joints and reapply additional elastomeric coating with better detailing at known crack areas.
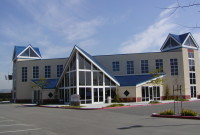
CHURCH INVESTIGATION – Assisted builder in identifying source of leaks within this church located in Hayward, California. Building was fairly new and was leaking adjacent to a few windows within the cement plaster clad walls. Isolation testing was performed to identify the source of the infiltration. Water was noted to be entering through the perimeters of the window frames at failed sealant joints. The sealants had not properly been bonded to the window substrate and in some instances the sealant joint was not sufficiently sized to allow for the proper sealant profile. Recommendations were made to inspect the sealants and to replace the caulking as necessary to keep water from accessing the outside perimeter of the window frames.
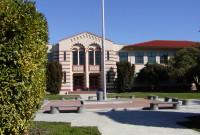
LITIGATION SUPPORT AT HAYWARD HIGH SCHOOL – Represented sealant installer on construction defect claim regarding water infiltration into building structure through the exterior cladding. Renovation and new construction on this high school located in Hayward California consisted of the exterior application of a direct applied exterior finish system commonly referred to as DEFS. This finish system is directly installed over an exterior gypsum sheathing system, which is considered a barrier system where water is required to be shed of the exterior finish. Our office represented the sealant installer who performed the caulking between the windows and the DEFS. The case was resolved through settlement discussions with all parties involved.
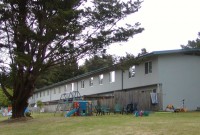
US COAST GUARD HOUSING – ACI collaborated with Industrial Hygiene firm in addressing the source of interior moisture contributing to substantial amounts of interior mold growth on 50+ year old military apartment housing. Interior moisture related to a number of current conditions, but was not related to water entry through the exterior walls. The structure had recently been through a renovation process consisting of single glazed window replacement with retrofit insulated windows and coating of the exterior stucco walls with an elastomeric coating system. The new window systems and elastomeric coating on top of decades of paint applications minimized the ability of the exterior walls to breathe. The renovation processes had resulted in inhibited air flow within the units, particularly the end units with large exterior wall areas. Remediation consisted of the addition of mechanical ventilation within units to help circulate air, along with tenant education on how to minimize interior moisture build-up.
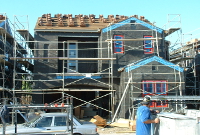
NEW HOME DEVELOPMENT – Major California homebuilder hires Aquatech Consultancy, Inc., to perform spot-checking on various home projects to check the integrity of the window installations within their cement plaster and wood sided homes. The sample project pictures noted here are typical of the process where a home is randomly selected and most all windows within the selected home are tested during the stage of the building paper installation, prior to installation of finishes. ASTM E1105 performance water tests are initiated by creating a negative pressure chamber on the interior framing behind the windows. The chamber is depressurized and monitored to meet the design pressure requirements for water infiltration resistance as established by the builder and designer. The primary focus of the testing is at the interface of the window and the adjacent flashing and building paper. Based on the results of this testing, ACI has provided further recommendations for window integrations, which this builder is instituting on all projects. ACI still comes out to current projects and performs spot checking as requested, but the success rates for window tests that pass are greater now than during the initial involvement in 2002.
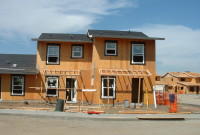
SOLANO BEACH LONG-TERM CARE – Provided assistance to plastering contractor regarding water infiltration problems in a newly constructed office park in Solano Beach, California. Exterior building components consisted of cement plaster (stucco), masonry cladding, aluminum panel cladding, storefront window systems, and various aluminum cladding components. Water infiltration was noted through the masonry wall and plaster wall systems, which incorporate a cavity drainage system as opposed to the aluminum panels, which created a barrier system. The heavy reliance on aluminum reveals within the cement plaster allowed excess water into cavity drainage system.